8 notable developments in software-defined manufacturing
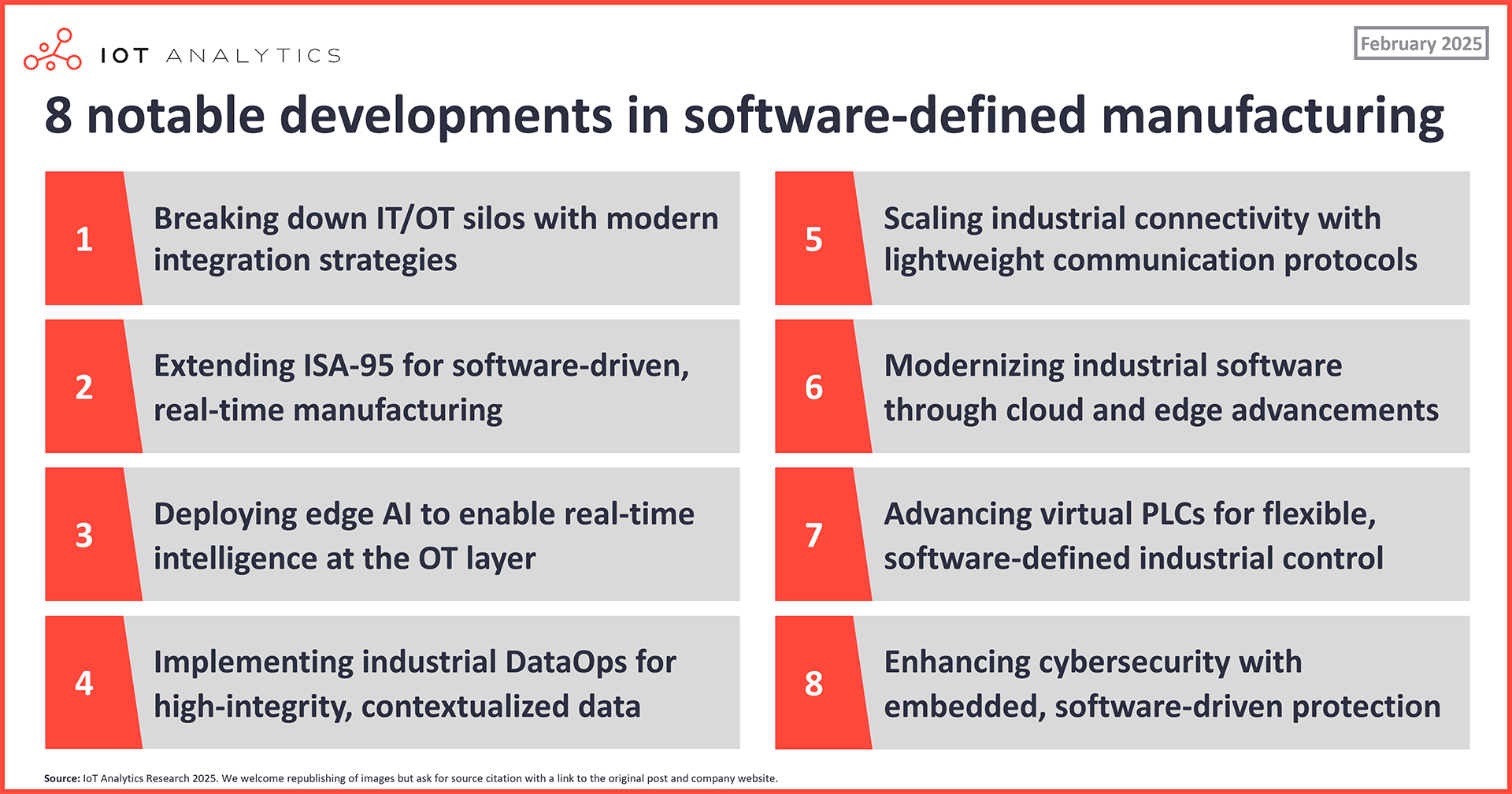
In short
- Scalability, automation, and serviceability are the top 3 paradigms that are shaping factories of the future.
- Underpinning these paradigms is software, and it is notable that software-defined manufacturing is increasingly replacing rigid, hardware-centric automation.
- The IoT Analytics team shares 8 notable developments in software-defined manufacturing based on its research and observations at major industry technology exhibitions.
Why it matters
- For industrial software vendors: As manufacturers adopt modern edge computing, cloud integration, and software-defined automation, vendors must support modular architectures, real-time data processing, and API-driven interoperability to stay competitive.
- For manufacturers: To stay competitive, manufacturers should adopt software-defined solutions that seamlessly connect IT and OT. Virtual PLCs, industrial DataOps, and lightweight communication protocols increase flexibility, reduce downtime, and improve data-driven decision-making.
Insights derived from
- SPS Fair 2024: The Latest Industrial Automation Trends
- IT/OT Convergence Insights Report 2024
- Industrial Connectivity Market Report 2024–2028
- Virtual PLC and Soft PLC Market 2024–2030
Intro
Manufacturers prioritize scalable, automated, and interoperable software-driven factories. In a 2024 IoT Analytics and Microsoft joint survey of technology leaders from 500 manufacturers, respondents were asked what their tech stack priorities are over the next 3–5 years. The results revealed the 6 paradigms shaping the factories of the future:
- Scalability – 72% of respondents want a seamless ability to expand and scale down in response to market demand.
- Automation – 70% of respondents want technology to perform tasks previously done manually.
- Serviceability – 67% of respondents want ease with which factory equipment and systems could be maintained and repaired to help overcome skill labor gaps.
- Accessibility – 62% of respondents want to provide easy access to factory data and controls using user-friendly interfaces and tools.
- Modularity and flexibility – 58% of respondents want processes and systems to be designed for easy reconfiguration and adaptation to new products or processes.
- Interoperability – 58% of respondents want differing systems, devices, and applications to work seamlessly, from the factory floor to the cloud.
Software underpins these paradigms, enabling manufacturers to scale, automate, and modernize operations while ensuring serviceability, accessibility, and interoperability across their ecosystems. The shift toward software-defined manufacturing replaces rigid, hardware-centric automation with flexible, software-driven architectures, AI-powered intelligence, and modular industrial platforms that optimize control and data flow. This shift is reflected in 8 key developments shaping software-defined manufacturing today.
8 notable developments in software-defined manufacturing
Below are the 8 developments in software-defined manufacturing the IoT Analytics team has noted through its continued coverage of Industry 4.0 topics, including attendance at leading tech fairs, conferences, and exhibitions such as SPS 2024 and Hannover Messe 2024 and recent research on industrial connectivity, IT/OT convergence, soft and virtual PLCs, industrial software, among others.
1. Breaking down IT/OT silos with modern integration strategies
Manufacturers push IT/OT convergence to overcome integration challenges. IT/OT convergence is the integration of IT and OT technologies, processes, and organizational structures to optimize industrial operations. Recently, IoT Analytics shared the 27 themes defining IT/OT convergence based on interviews with experts operating at the crossroads of IT and OT—including personnel at industrial hardware and software OEMs, system integrators, and consultants—as shown below.
Manufacturers are driving the demand for IT/OT convergence, largely due to their IT and OT integration challenges. Deploying innovative solutions for specific use cases within plants is often hindered by legacy systems, disconnected IT and OT teams, and complex integration tasks. Additionally, issues such as incompatible standards, security concerns, and the long life cycles of OT equipment add further complexity. Approaches like agile development, DevOps, and modular design, along with technologies such as AI, low-code platforms, containerization, data orchestration, and APIs, help make OT systems easier to build, update, and connect.
These factors push manufacturers to seek more unified, integrated solutions that bridge the IT and OT gap.
Example: At SPS 2024, US-based industrial automation company Rockwell Automation demonstrated its DataOps tool FactoryTalk DataMosaix, specifically the App Builder module. App Builder allows users to configure dashboards with drag-and-drop visualization tools, access data from cloud platforms or on-premise repositories, and generate automated reports. Rockwell representatives emphasized that DataMosaix can serve as a foundation data source for other software like Plex MES or PTC ThingWorx.
2. Extending ISA-95 for software-driven, real-time manufacturing
Manufacturers are modernizing ISA-95 with real-time, modular integrations. ISA-95 is an international standard released in 2000 for integrating enterprise and control systems in industrial automation. A common implementation of the ISA-95 principles that formed soon after the standard’s inception is best characterized as a hierarchical pyramid, representing a structured framework for organizing, categorizing, and managing equipment, as shown below.
The ISA-95 pyramid has generally remained unchanged over the years and continues to define the hierarchical structure that governs the relationship between enterprise IT and industrial automation systems. However, how manufacturers implement and extend the pyramid in modern industrial environments has evolved significantly.
The emergence of enabling technologies like edge computing, cloud architectures, and API-driven interoperability has driven the need for variations and extensions to the traditional ISA-95 hierarchy. Instead of rigid, layer-based communication between sensors, control devices, and other applications, manufacturers are adopting edge/cloud-driven and distributed-edge-driven architectures, including de-coupled event-driven data exchange (publish-subscribe) to improve scalability, flexibility, and responsiveness. These changes enable more modular, loosely coupled IT/OT integrations, where data from manufacturing systems is dynamically contextualized, processed, and consumed.
Example: US-based industrial edge platform provider Litmus offers Litmus Edge, an industrial edge platform that standardizes and contextualizes OT data for seamless integration with cloud services and enterprise applications. By leveraging edge computing and API-driven interoperability, it enables event-driven data exchange and modular IT/OT integration, enhancing scalability and flexibility. Notably, Litmus Edge integrates with Microsoft’s Azure Manufacturing Data Solutions, using the ISA-95 data protocol to structure factory data within a knowledge graph, extending ISA-95 to support modern, distributed architectures.
*Note: IoT Analytics plans to publish the Industrial Automation Projects Report and Database this month. Those interested in accessing these reports when they are released can sign up for IoT Analytics’ IoT Research Newsletter by clicking below.
3. Deploying edge AI to enable real-time intelligence at the OT layer
Edge AI enhances real-time processing and decision-making. The landscape of IPCs and IoT gateways is undergoing a significant shift, with a new trend toward more edge computing capabilities integrated with AI accelerators to run AI workloads. Referred to as edge AI, this shifts intelligence closer to OT data sources through software running on these edge devices. This trend is driven by the need for real-time data processing and decision-making capabilities near the source of data generation, reducing latency and bandwidth usage. By deploying and managing AI models through software frameworks supported by AI accelerators (e.g., GPUs or NPUs), edge AI enables real-time inference, driving faster, data-driven decision-making at the OT edge.
Example: At SPS 2024, Eurotech (an Italy-based edge computing and industrial IoT solutions provider) showcased multiple edge AI IPCs, including its ReliaCOR 33-11 fanless IPC/IoT gateway running on NVIDIA’s Jetson AGX Orin single-chip edge AI computer. These edge AI IPCs include Eurotech’s Everyware Software Framework (ESF), an open-source Java middleware for IoT gateways optimized for multi-AI model loading/testing and edge AI application development.
4. Implementing Industrial DataOps for high-integrity, contextualized data
DataOps is emerging as a top industrial connectivity trend. IoT Analytics research has found that the #1 general industrial connectivity trend is the growing importance of DataOps. DataOps is a software-driven approach for industrial data management, focusing on data quality and modeling.
Manufacturing landscapes are complex, with numerous sensors, machines, and systems interacting. By leveraging data pipelines, orchestration engines, data governance rules, and tools like low-code, DataOps transforms raw data into high-integrity, contextualized data. A Unified Namespace (UNS) can serve as a foundational component within DataOps, providing a structured data framework that ensures consistent and scalable information flow across machines, enterprise applications, and cloud systems. By leveraging UNS within DataOps, manufacturers can enhance data accessibility, reduce integration complexity, and enable more effective AI-driven decision-making.
Example 1: US-based industrial DataOps software company HighByte offers HighByte Intelligence Hub, an industrial DataOps solution that enables standardized data modeling for manufacturing environments. The Hub supports the creation of real-time and asset model data from various edge data sources, including machine data, transactional data, and time-series (historical) data. Additionally, it can populate a Unified Namespace structured to the ISA-95 hierarchy, providing a standardized framework for organizing and contextualizing industrial data.
Example 2: Germany-based industrial software company Cybus offers Cybus Connectware, a DataOps platform that enables a Unified Namespace for manufacturing environments. It collects, standardizes, and distributes real-time data across OT and IT systems, aiding seamless integration and eliminating data silos. By structuring industrial data into a centralized, scalable architecture, Connectware aims to enhance accessibility, optimize data flow, and accelerate digital transformation efforts.
5. Scaling industrial connectivity with lightweight communication protocols
MQTT brokers enable scalable and reliable industrial data exchange. Working alongside DataOps to enable industrial connectivity are message brokers, like MQTT. MQTT brokers are lightweight publish-subscribe intermediaries that manage real-time data exchange between systems. They facilitate scalable, event-driven communication architectures with software-driven capabilities handling message routing, topic management, and quality of service controls. This ensures efficient and reliable data flow across diverse industrial systems.
MQTT brokers play a critical role in reliably handling large amounts of data, and there are a plethora of MQTT brokers in the market, some open source and each with distinct advantages.
Example 1: Germany-based HiveMQ offers a leading eponymous closed-source MQTT broker running on the Java virtual machine and catering to verticals such as connected cars, energy, pharma, and others. It has an open API for third-party integration and prebuilt extensions for enterprise systems such as Kafka, SQL, and NoSQL. The broker can be deployed on private, hybrid, and public clouds like AWS and Microsoft Azure. The enterprise version can scale up to 200 million connected devices.
Example 2: US-based industrial software company EMQ Technologies offers EMQX, another MQTT broker designed for large-scale IoT applications. The vendor EMQ claims it can support over 100 million connections in a single cluster and processes millions of MQTT messages per second with low latency. EMQX supports multiple protocols like MQTT, HTTP, QUIC, and WebSocket, enabling the connection of devices using different protocols.
6. Modernizing industrial software through cloud and edge advancements
Cloud and edge computing enable scalable, software-driven manufacturing. Software-defined manufacturing is driven by the adoption of cloud-native and edge-computing paradigms, shifting from monolithic to modular and scalable software architectures. In the cloud, software powers scalable applications and centralized orchestration, while at the edge, it drives real-time control and localized intelligence. Together, they form an edge-cloud continuum that connects and optimizes operations across distributed industrial systems.
Example: Germany-based engineering and technology company Bosch sells Nexeed, a modular manufacturing execution system (MES) aimed at providing end users with flexibility in how it is deployed. Customers may choose to keep critical components, such as line control, execution, or traceability, at the edge but opt to run dashboards and other non-critical applications from the cloud.
7. Advancing virtual PLCs for flexible, software-defined industrial control
Virtual PLCs enable flexible, software-driven industrial control. Virtual PLCs (vPLCs) represent a software-centric shift in industrial control, allowing control logic to run independently of proprietary hardware. By leveraging virtualization, containerization, and other software technologies, vPLCs support software-enabled rapid updates, remote management, and dynamic resource allocation.
Example: After a few years of slow progress in overcoming hurdles to become the industry norm, such as lacking support for key technical requirements, as shown in the graphic above, the virtual PLC is seeing significant advancements. At SPS 2024,CODESYS previewed Virtual Safe Control, a virtual safety controller compliant with the IEC 61508 SIL3 standard. This enables virtualized safety controllers that are independent of specific hardware platforms.It uses dual-channel execution via “Coded Processing” to enhance safety, incorporating diversified encoding and continuous control flow monitoring during runtime. Additionally, it supports fieldbus systems like PROFIsafe and EtherCAT Safety.
8. Enhancing cybersecurity with embedded, software-driven protection
Software-driven security enhances protection in smart manufacturing. In software-defined smart manufacturing, where the ever-growing number of connected devices presents increased cybersecurity risks, software-based security embedded across the entire architecture and integrated into the software stack, governing data flows and system interactions has become paramount. This has driven the development of several software-driven approaches, including dynamic access controls, real-time threat detection and reporting, encryption protocols, and policy enforcement, enabling continuous monitoring, rapid response to vulnerabilities, and adaptive security measures tailored to evolving industrial threats.
Example: At SPS 2024, US-based networking, security, and connectivity products provider Belden Inc. showcased recent improvements in its Horizon cloud platform, including its Beldon Horizon Network Insights (BHNI) app, which allows IT to monitor all OT devices from the cloud. BHNI automatically sniffs network data to detect and report anomalies, security, and performance issues via a simple dashboard.
Analyst takeaway
The shift toward software-defined manufacturing is accelerating as manufacturers prioritize automation, scalability, and interoperability in their tech stacks. IT/OT convergence, industrial DataOps, cloud-edge architectures, and virtual controllers are fundamentally reshaping industrial automation, driving a move away from rigid, hardware-dependent systems.
For industrial software vendors, success will require fully embracing API-driven, containerized, and modular architectures that enable real-time data processing and seamless interoperability across IT and OT environments. The shift is not just about selling software—it is about building open, scalable ecosystems that manufacturers can integrate with their existing operations. OT vendors should take inspiration from IT platforms like Salesforce, ServiceNow, and Databricks, which have built API-first, data-centric ecosystems that seamlessly connect multiple enterprise applications. A similar approach in industrial automation would unlock greater flexibility, faster deployment cycles, and improved data contextualization.
For manufacturers, investing in software-defined automation is no longer optional—it is a competitive necessity. Those that fail to modernize their control architectures, connectivity strategies, and data pipelines risk being left behind in an era where agility and intelligence define industrial success. Companies in the automotive sector—particularly EV-first players like Tesla—are at the forefront, using software-defined MES, edge-driven analytics, and AI-powered quality control to increase production agility. Similarly, Foxconn has set the benchmark for IT-OT integration at scale, leveraging cloud-driven MES, software-defined robotics, and digital twins to reconfigure factories based on shifting market demands.
The lesson is clear: Industrial automation can no longer be hardware-first. The future belongs to software-defined, real-time, and adaptive manufacturing ecosystems that mirror the success of IT in building flexible, API-driven architectures.
Disclosure
Companies mentioned in this article—along with their products—are used as examples to showcase market developments. No company paid or received preferential treatment in this article, and it is at the discretion of the analyst to select which examples are used. IoT Analytics makes efforts to vary the companies and products mentioned to help shine attention to the numerous IoT and related technology market players.
It is worth noting that IoT Analytics may have commercial relationships with some companies mentioned in its articles, as some companies license IoT Analytics market research. However, for confidentiality, IoT Analytics cannot disclose individual relationships. Please contact compliance@iot-analytics.com for any questions or concerns on this front.
Further reading
Related publications
You may also be interested in the following reports:
- IT OT Convergence Insights Report 2024
- Industrial Connectivity Market Report 2024–2028
- Hannover Messe 2024—the latest Industrial IoT/Industry 4.0 Trends
Related articles
You may also be interested in the following articles:
- IoT 2024 in review: The 10 most relevant IoT developments of the year
- Virtual PLCs: Can they become the industry norm by 2030?
- The industrial software market landscape: 7 key statistics going into 2025
Subscribe to our newsletter and follow us on LinkedIn and Twitter to stay up-to-date on the latest trends shaping the IoT markets. For complete enterprise IoT coverage with access to all of IoT Analytics’ paid content & reports, including dedicated analyst time, check out the Enterprise subscription.
Leave a Comment